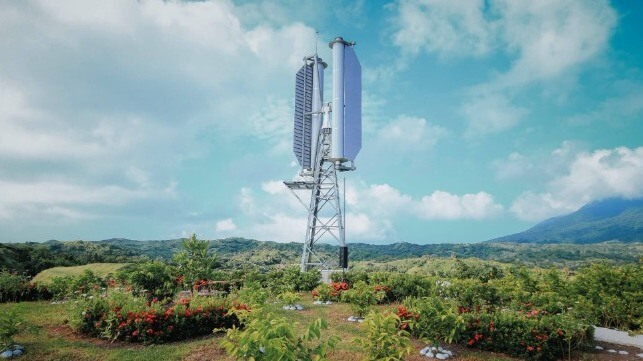
New Technology Could Advance Maritime Wind Propulsion
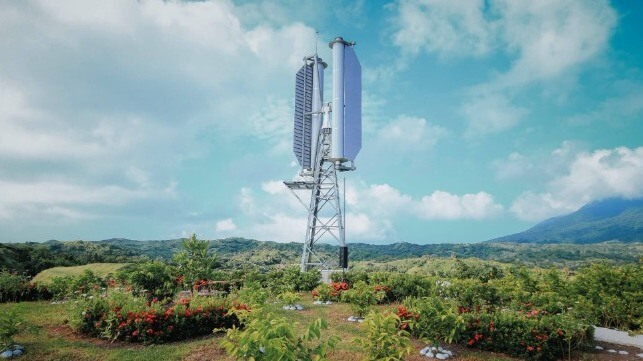
Harry Valentine
Through the 1980’s, College of Michigan professor of enterprise Dr. C. K. Prahalad’s treatise entitled “Competing for the Future” concentrated on “the convergence of systems.” There is possible to incorporate modern technological developments to progress maritime wind propulsion, and technological know-how from Sweden, Japan, the United states of america, Germany and in the Uk features this sort of a risk.


Introduction


Through the early 1980’s, physics professor Brad Blackford entered a windmill driven boat in a competitiveness for wind-run sail boats at Halifax, Canada. He sailed his boat right into a headwind and received the race, using an angled axial-movement wind turbine that directly drove a small boat propeller. Through afterwards decades, Blackford improved on the concept and achieved a velocity of 8 knots though sailing straight into a headwind. He sailed his wind turbine boat along the east coast of the United States in winds of moderate speed, the wind turbine and propeller having above-speed and cavitation restrictions.


Superior Efficiency at Small Velocity


Quite a few inventors have experimented with flukes to enhance minimal-velocity propulsive effectiveness of little boats. A Swedish company named “Dol-prop” markets this sort of a products which is based mostly on the tail fin of a dolphin. Lovers have made both equally vertical and horizontal mechanical tail fins to attain bigger performance propulsion. The demonstration of the engineering on smaller boats suggests opportunity to create significant-scale versions of mechanical tail fin propulsion know-how, likely driven by vertical-axis storm able wind turbine engineering making use of the Magnus outcome, that originated from Japan.


The cylindrical Magnus-effect vertical-axis rotors of the storm turbine able of spinning at intense rotational speeds though exerting force of a lever to generate a central travel shaft that carries particularly significant torque at reasonably very low RPM. An excellent long run thought would mix the power properties of such a turbine with a huge-scale mechanical fin able of propelling a big vessel sailing westbound throughout the North Atlantic into extreme headwinds that happen for the duration of the latter aspect of each yr. An option layout would use a person of two competing models of well-demonstrated vertical-axis propulsion technologies.


Vertical-Axis Turbine


Whilst vertical-axis turbines convert energy considerably less effectively than horizontal-axis turbines, they can be built with a reduce heart-of-gravity, which gives stability pros in mobile software. The current innovation of setting up Magnus-impact rotors to vertical-axis wind turbine design permits for operation in extreme high-speed wind situations. This kind of rotors are at the moment being manufactured for the maritime sector as an alternate to sails. There is scope to adapt the similar rotors on deck-mounted, huge-scale vertical-axis turbines, with opportunity to operate upper and decreased team of rotors on the same assembly.


The combination of detachable railway-style wheels riding on a curved rail would carry the weight of the rotating turbine assembly, with each rotor equipped with a brake and an electric or air-stress starter motor along with the trailing fin thought that Challenergy pioneered in Japan. Magnus-outcome vertical-axis wind turbine know-how promises to resolve operational issues of before vertical-axis wind turbine designs in severe wind speeds. The lessen centre-of-gravity makes it possible for for larger sized scale building than horizontal-axis tower-mounted wind turbines intended for maritime propulsion.


Horizontal-Axis Turbine


The wind turbine field has concentrated on developing horizontal-axis turbines mounted on towers to crank out electric energy for the utility grid, with the major three-bladed offshore turbines rated at 14 MW (18,700 horsepower) making use of blades of 354 ft in diameter. These kinds of a electric power degree is the result of a lot of successive decades of ongoing investigate and development, with a hurricane capable edition of the technologies having now been designed. Horizontal-axis wind turbines on towers have been made use of for smaller-boat propulsion applying a mechanical equipment transmission.


A wind turbine rated at 500 kW (670 horsepower) in a wind speed of 30 mph and spinning at 240 RPM would deliver practically 15,000 lb-ft of torque. A planetary gearbox could raise rotational pace to 2,400 RPM at 1,500 lb-ft of torque to be transmitted via 90-degree spiral bevel gears and concentric counter-rotating vertical shafts.


Upcoming Wind Turbine Enhancement


The improvement of storm able vertical-axis wind turbine know-how in Japan offers opportunity to undertake additional research into establishing a simple and aggressive multi-megawatt, mega-scale edition able of furnishing maritime propulsion. Vertical-axis know-how allows the turbine to straight drive vertical-axis propulsion technology, with the choice of planetary gears to alter relative rotational speeds or to use crank and connecting rod technological know-how to drive large-scale mechanical tail fin propulsion technological know-how. The central shaft of a two-degree mega-scale typhoon turbine rotating at 90 RPM carrying 250,000 lb-ft of torque would supply just around 4,300 horsepower or 3,200kW to a vertical-axis propeller.


Voith-Schneider Propulsion


The vertical-axis Voith-Schneider propulsion engineering is nicely verified in tugboat programs and could be pushed by a vertical-axis wind turbine. Changing the vertical blade angle to the neutral zero-thrust placing would permit for operation of a wind turbine with negligible commencing torque. Although extending the height of the propulsion blades would increase maximum propulsive thrust, these kinds of a modification would improve bending loads on the blades. There may perhaps be need to have to undertake investigate into the benefit of working with each higher and lower-level disc plates to safe every single vertical propulsion blades at the two ends on a mega-scale model.


It is probable for vertical-axis wind turbine know-how to drive the Voith-Schneider working with possibly direct gearless drive or by installing a vertical-axis planetary gear method between the wind turbine and the propulsion device. The thruster blades include pivots and linked technologies that involve normal inspection and maintenance. A competing axial-movement propeller that operates vertically would involve less repeated inspection and routine maintenance thanks to the absence of pivots and linked technology. A wind-turbine run vessel assigned to trans-ocean sailing would call for a high degree of very long-time period reliability together with relieve of inspection and maintenance of the electricity and propulsion process.


Vertical-axis axial-circulation propeller


A British organization gives a vertical-axis axial-stream propeller mounted inside a duct that involves steerable capability. While a self-starting up vertical-axis wind turbine could right push a vertical-axis propeller, there would most likely be have to have to put in overdrive gearing involving a sluggish-turning wind turbine and speedy turning propeller. Planetary gear methods primarily based on the combination of ring gears and various parallel earth gears would capable of enduring sustained superior torque loads at very low rotational velocity. A vertical axis propeller crafted to surplus diameter with variable pitch blades would function at high performance at comparatively minimal RPM.


Downstream of the propeller, a horizontal area of rectangular duct with variable cross-sectional outlet would permit for adjustment of sailing velocity. An array of multiple deck-mounted vertical-axis turbines that each individual drive a vertical 3-throw crankshaft may perhaps be connected to each individual other by tension cables and drive a solitary vertical-axis propeller. Just about every vertical-axis turbine may possibly alternatively generate its have vertical-axis propeller with a duct that brings together with other ducts at the vessel’s stern. Variable-pitch blades would adjust to a assortment of electrical power output and control wind turbine velocity although sailing in excess of prolonged distances in highly effective wind disorders.


Mechanical Tail Fin


A vertical-axis turbine would drive a vertical crank shaft with two throws spaced 180-levels aside. The crank shaft would drive a pair of connecting rods attached to the activation levers of a pair of parallel spring-loaded vertical mechanical tail fins. The ahead end of every single lever would connect to vertical-axis rudder-kind pivot shafts secured to the vessel hull. Every single connecting rod would attach to each and every lever at a vertical-axis pivot found in between the tail fin and the rudder kind shaft. Through procedure, the tail fins would shift cyclically in opposite directions to provide propulsion.


https://www.youtube.com/observe?v=xWAKtbiyTxc


A long term big-scale variation of the parallel tail fin strategy would most likely swap the spring-loaded procedure with the combination of forward and rear vertical-axis crank shafts established 90-levels aside. A ahead established of upper and reduce connecting rods would connect to the tail fin’s leading region while trailing connecting rods would connect to the tail fin’s trailing spot. Putting in the mechanical tail fins within a rectangular duct with variable region outlet would probable boost propulsive efficiency when skill to alter sailing velocity. A mechanical linkage would hook up the vertical-axis turbine(s) to the propulsion process.


Conclusions


About the past ten years, hurricane/hurricane able wind turbines have been formulated in the two horizontal-axis and vertical-axis configurations. When combined with similar developments in mechanical tail fin propulsion and vertical-axis axial-circulation propellers, these systems supply new potential clients in tall wind-driven vessels that would be restricted to sailing routes and ports with unrestricted vertical top clearance. A long run mega-scale Magnus-influence vertical-axis wind turbine could immediately push a vertical-axis axial-movement propeller with variable-pitch blades.

The opinions expressed herein are the author’s and not automatically those people of The Maritime Government.